Themen des Artikels
Um Themen abonnieren und Artikel speichern zu können, benötigen Sie ein Staatsanzeiger-Abonnement.Meine Account-Präferenzen
Röser lotet die Grenzen des 3D-Drucks aus
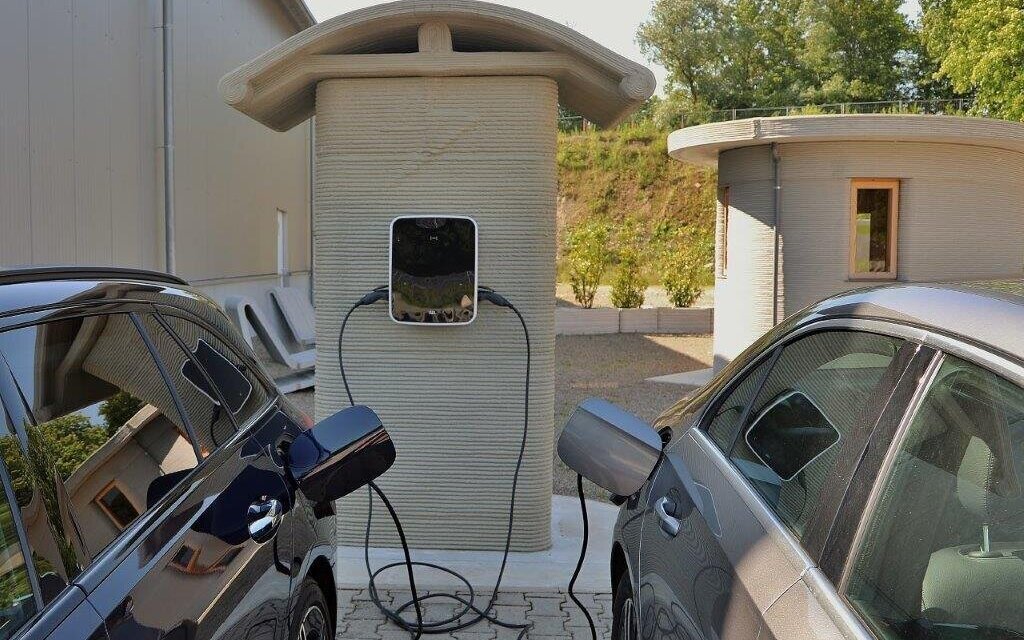
Auf dem Firmengelände von Röser stehen einige Pilotobjekte, die aus dem Drucker stammen. Darunter auch eine E-Ladesäule.
Röser)Laupheim. Das Gelände des Fertigteileherstellers Röser in Laupheim (Landkreis Biberach) ist auf den ersten Blick unspektakulär. Erst auf den zweiten Blick fallen Sitzelemente, geschwungene Pflanzkübel, eine Ladesäule und sogar ein kleines Gebäude auf. Alle aus Beton gefertigt, der meist eine geriffelte Struktur aufweist. „Wir zeigen hier, was man im 3-D-Betondruck bereits heute für den Alltag herstellen kann“, erklärt Marcel Förderer. Er ist Teil des Teams, das für Rösler neue Produkte im 3-D-Druckverfahren entwickeln und damit neue Märkte erschließen soll.
Röser baut Fertigteile für den Tiefbau und Infrastrukturprojekte
Eigentlich ist die Röser-Gruppe für die Massenproduktion von Rohren, Schächten sowie für viele Tiefbauprojekte bekannt. Die Firmengruppe mit Sitz in Essingen bei Aalen beschäftigt rund 200 Mitarbeiter. Weitere Standorte sind in Dürmentingen, Krauchenwies und Steißlingen, wo Fertigteile für Tiefbau und Infrastruktur entstehen. Das Werk in Ellwangen produziert Fertigteile für den Agrar- und den Hochbau. Zudem gibt es einen eigenen Maschinenbaubetrieb.
„Die Geschäftsführung sieht im 3-D-Druck eine Technologie, mir der man sich frühzeitig beschäftigen muss“, erklärt Dennis Bräunche, verantwortlich für den Vertrieb. In einem ersten Schritt prüft das Unternehmen, ob 3-D-Verfahren eine Alternative für die herkömmliche Produktion von Fertigteilen darstellen könnten. Zwar ist der 3-D-Druck noch teuer. „Doch die Technologie eröffnet einfach völlig neue Gestaltungsmöglichkeiten“, betont Förderer. So können die Röser-Spezialisten beispielsweise ganze Wände mit Reliefs oder Firmenlogos gestalten. Solche Sonderanfertigungen sind mit herkömmlichen Methoden sehr aufwendig oder gar nicht realisierbar.
Ein Drucker steht in einer eigens errichteten Halle in Laupheim. „Damit sind wir von Witterungseinflüssen unabhängig“, erläutert Förderer. Produziert werden Elemente für Gebäude, zur Landschaftsgestaltung oder für Außenanlagen. Der wirkliche Aufwand ist die Planung und Programmierung. Der eigentliche Druck erfolgt oft in wenigen Stunden.
„Die Kunden müssen von den neuen Möglichkeiten erst noch überzeugt werden. Aber das Interesse wächst“, freut sich Vertriebsmanager Bräunche. Landschaftsgestalter und experimentierfreudige Architekten seien von den planerischen Möglichkeiten begeistert, die die neue Technologie bietet. Der 3-D-Druck erlaubt geschwungene Formen, die bisher nur kostspielig oder gar nicht umsetzbar sind. „Zudem benötigen wir weniger Zeit und Material. Das macht sich auf der Kostenseite bemerkbar“, erklärt Förderer. Nun wird der Baustoff durch die steigenden Produktionsmengen günstiger. „Am Anfang hatten wir mit Gebinden zu je 25 Kilogramm gearbeitet. Inzwischen liefern die Zementwerke Silofüllungen von bis zu 30 Tonnen an.“
Die Pioniere müssen auch verschiedene Softwarelösungen unter einen Hut bringen, die nicht miteinander kompatibel sind. Bisher wurde in Bauprojekten mit verschiedenen Lösungen gearbeitet, erklärt Bauingenieur Förderer. Doch nun müssen die einzelnen Bereiche und Gewerke an einem gemeinsamen Entwurf arbeiten und ihn fortschreiben.
Für gedruckte Elemente gibt es keine definierten Normen
Eine weitere Hürde für die Pioniere: Für gedruckte Elemente gibt es keine definierten Normen. Die Behörden müssen sich bei der Freigabe an vergleichbaren klassischen Elemente orientieren. Das erfordere eine gewisse Offenheit und Flexibilität in den Amtsstuben, so die Röser-Experten. Und erlangt ein Architekt in Baden-Württemberg dafür endlich die Genehmigung, ist das damit längst nicht allgemeingültiger Standard. „So kann es passieren, dass die 3-D-Druckteile auf Baustellen in Nordrhein-Westfalen erneut überprüft werden müssen, weil dort andere Bauvorschriften gelten“, sagt Förderer. (auk)